Case Studies
Toyota’s Lean Manufacturing: A Process-Driven Model of Continuous Improvement
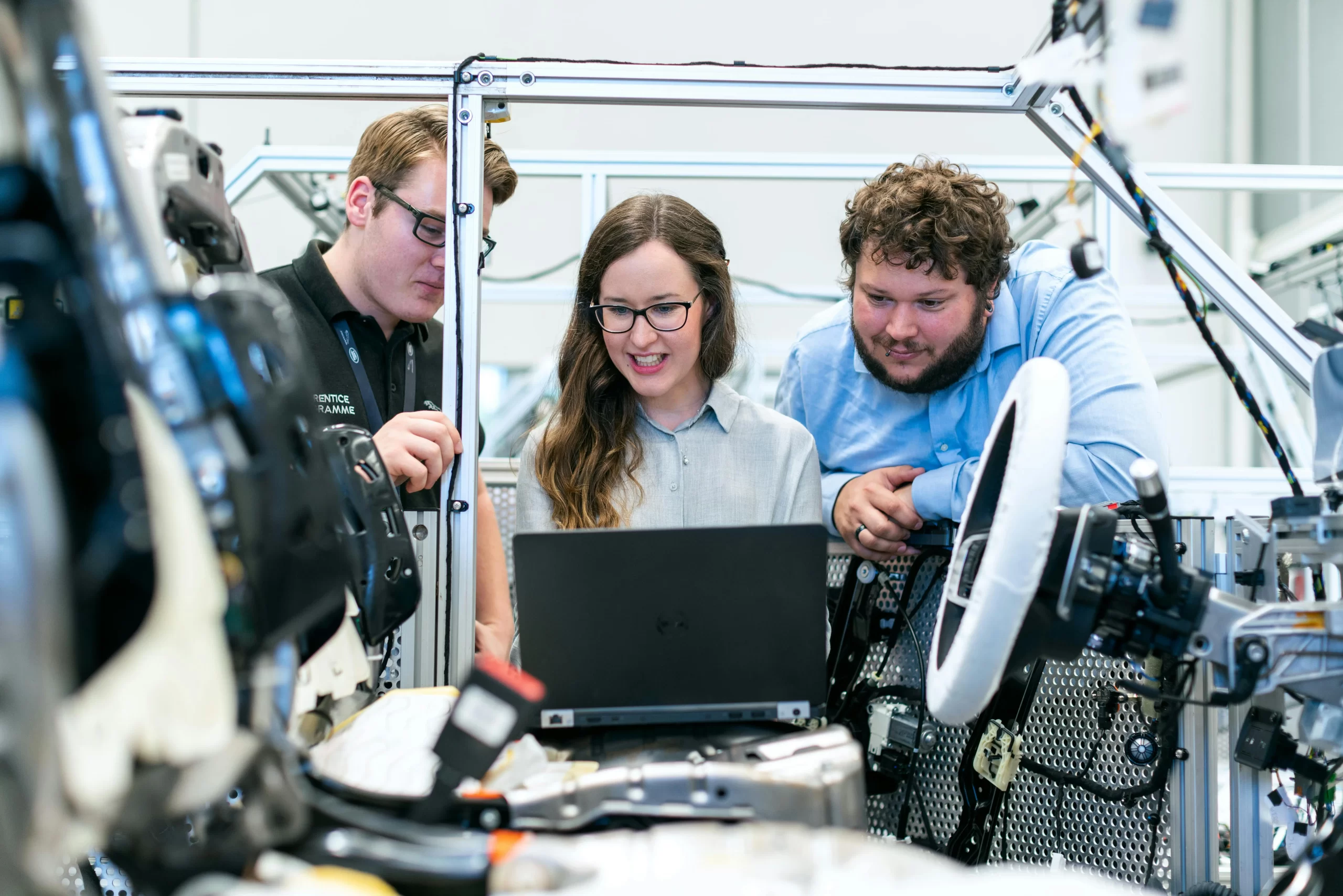
Toyota’s legendary Lean Manufacturing System (Toyota Production System – TPS) has transformed global manufacturing by prioritizing efficiency, waste reduction, and continuous improvement (Kaizen). Unlike traditional production models, Toyota’s lean approach focuses on maximizing value while minimizing waste, ensuring long-term sustainability and agility.
Taiichi Ohno, one of the architects of TPS, famously stated, “The more inventory a company has, the less likely they will have what they need.” This philosophy has shaped Toyota’s production strategy, emphasizing just-in-time (JIT) manufacturing, continuous learning, and total workforce engagement.
How Toyota’s Lean Manufacturing Model Drives Efficiency
Toyota’s success is built on core lean manufacturing principles that eliminate inefficiencies and enhance productivity:
- Just-In-Time (JIT) Production – Minimizing waste by producing only what is needed, when it is needed.
- Kaizen (Continuous Improvement) – Encouraging employees at all levels to contribute ideas for process optimization.
- Pull-Based Inventory System – Using real-time demand signals to control inventory replenishment.
- Error-Proofing (Poka-Yoke) – Designing processes to prevent mistakes before they happen.
Example: Toyota reduced production lead times by over 50% by implementing its Kanban system, which streamlined material flow and eliminated excess inventory.
Key Performance Indicators (KPIs) for Lean Success
Toyota’s lean model relies on precise metrics to track efficiency, cost reduction, and quality improvements.
- Cycle Time Reduction – Tracks how quickly products move through the production process.
- First Pass Yield (FPY) – Measures the percentage of products manufactured correctly without rework.
- Inventory Turnover Rate – Assesses how effectively inventory is managed.
- Defect Rates – Monitors product quality and identifies areas for improvement.
- Operational Equipment Effectiveness (OEE) – Ensures maximum utilization of machinery and resources.
Example: Toyota’s FPY rate is among the highest in the industry, ensuring minimal defects and near-perfect assembly-line efficiency.
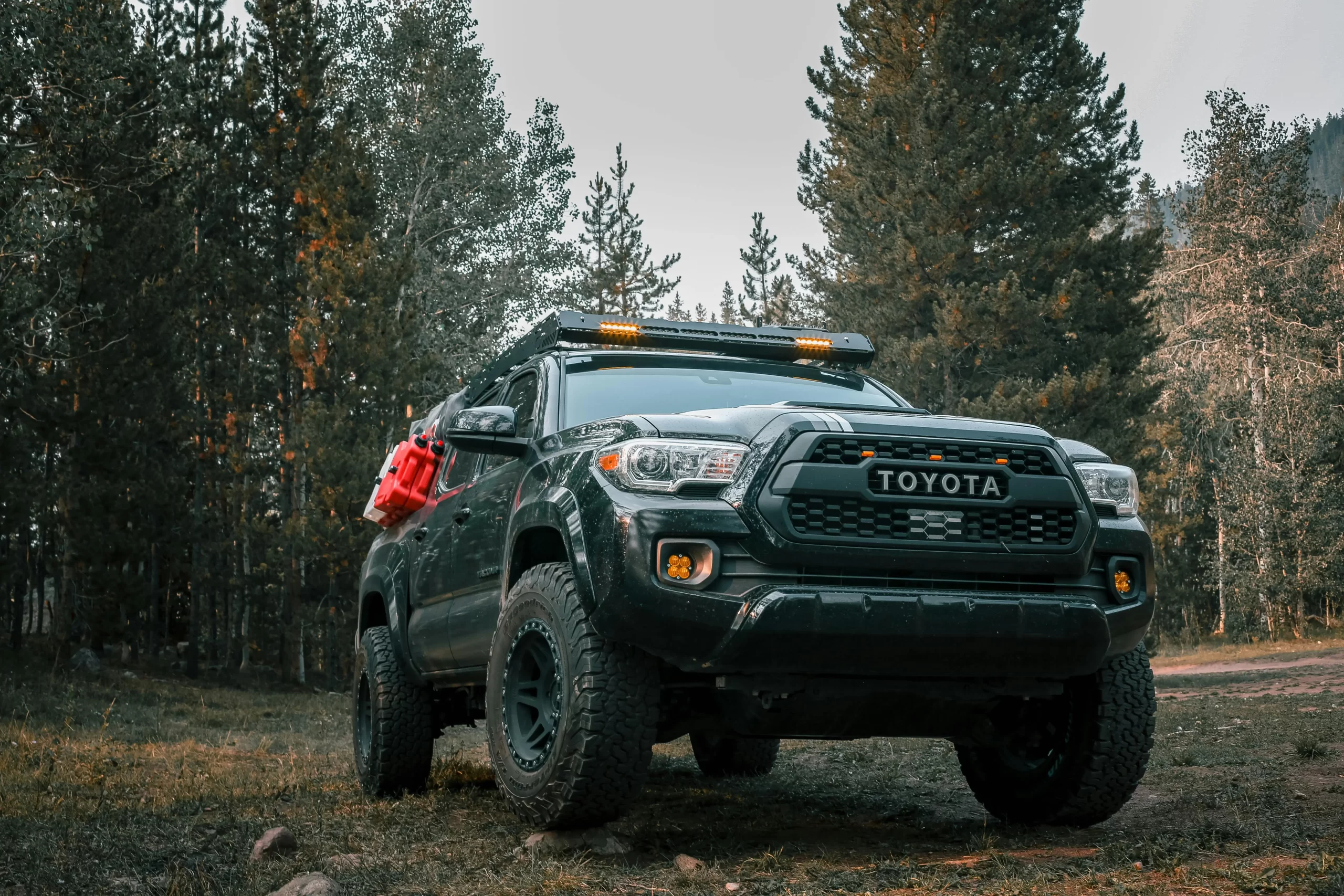
Gamification & Employee Engagement in Lean Processes
Toyota applies gamification and motivation-driven strategies to engage employees and drive lean culture adoption.
- Continuous Learning Challenges – Employees are encouraged to participate in Kaizen events to suggest process improvements.
- Visual Management Systems – Gamified dashboards track performance metrics and encourage competition among teams.
- Recognition & Rewards – Teams that contribute high-impact ideas receive company-wide recognition.
- Simulation-Based Training – Employees engage in real-world lean problem-solving through interactive workshops.
Example: Toyota’s Kaizen Award Program has led to thousands of employee-generated innovations, reducing production costs and enhancing efficiency.
Applying the Total Football Framework (TFT) to Toyota’s Lean Manufacturing Model
Toyota’s lean principles align closely with the Total Football Teams (TFT) Framework, which emphasizes fluid teamwork, dynamic role adaptability, and process efficiency.
- Role Flexibility & Workforce Optimization – Just as TFT players shift roles dynamically, Toyota’s employees are cross-trained to handle multiple tasks, reducing downtime and increasing efficiency.
- Real-Time Process Adjustments – TFT encourages on-the-spot tactical changes, similar to Toyota’s real-time workflow optimizations based on demand fluctuations.
- Collaborative Problem-Solving – TFT teams constantly adjust their gameplay, mirroring Toyota’s Kaizen-driven approach to iterative improvements.
- Data-Driven Decision Making – Like TFT’s reliance on performance analysis, Toyota uses lean metrics to refine operations and eliminate inefficiencies.
Example: Toyota’s introduction of automated quality inspections based on real-time data analysis mirrors TFT’s match analytics, ensuring optimal decision-making in both production and football strategy.
The Future of Lean Manufacturing at Toyota
Toyota continues to refine its lean principles to stay ahead in an evolving global economy:
- AI-Driven Predictive Maintenance – Using machine learning to prevent equipment failures before they occur.
- Sustainable Lean Practices – Enhancing eco-friendly manufacturing with minimal waste.
- Digitization of Lean Processes – Integrating IoT and automation for real-time process optimization.
- Agile Production Models – Expanding lean beyond manufacturing into agile-based product development.
Example: Toyota’s Smart Factory initiative integrates AI and IoT sensors to enhance operational efficiency and reduce energy consumption.
Final Takeaways: Why Toyota’s Lean Model Works
Toyota’s lean manufacturing system remains a benchmark for process-driven efficiency, continuous improvement, and workforce engagement.
- Lean principles minimize waste while maximizing value.
- KPIs drive efficiency, productivity, and long-term sustainability.
- Gamification enhances employee engagement and continuous learning.
- TFT-inspired adaptability ensures Toyota’s workforce remains agile and future-ready.
Toyota isn’t just building cars—it’s perfecting the art of lean efficiency. The challenge for other businesses: How can they implement lean methodologies to optimize their own processes?